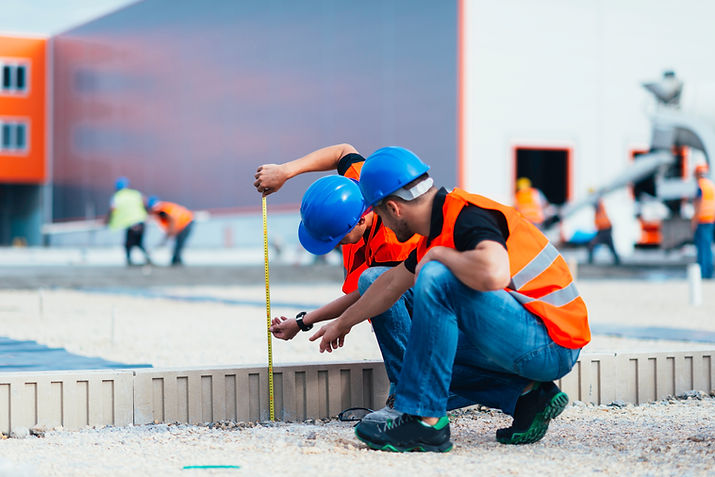
PRODUCT DESIGN CASE STUDY:
BESPOKE TABLET ENCLOSURE
BRIEF
This project was completed on behalf of Spud Construct, a UK company who are changing the face of the construction industry through the introduction of their extremely comprehensive construction project management tool. Aspects of their software based product relies on the use of the Morphotablet 2, a powerful biometric tablet capable of streamlining aspects of the construction industry, including fingerprint clock in and clock out.
​
Print My Part were tasked with creating a bespoke enclosure, capable of housing and securing the tablet. The end product would initially be manufactured in smaller batches of less than 100 units. With demand growing rapidly, the enclosure has now been 'tooled up' for mass production using the injection moulding process. The tablet stands are currently in use for access control at some of the largest construction projects in Europe.
DESIGN & DEVELOPMENT
The enclosure design was required to meet various objectives, such as:
​
-
Secure the tablet in a fixed location on site.
-
Allow quick and easy tablet removal using a hinged front and lock and key.
-
Provide connection of a charge cable during use (which cannot be removed unless unlocked).
-
Remove access to buttons when locked.
-
Provide suitable airflow and heat dissipation around tablet.
-
Provide water exit holes in the event of severe condensation.
-
Present a robust and durable aesthetic in-keeping with the use environment.
​
Once the initial concept exploration phase was complete, we quickly progressed onto Computer Aided Design software to begin developing the final product. Because of the initial modest quantity requirements, we opted for the Vacuum Casting production process in a resin which matched the robust properties of ABS. However, as Injection Moulding was the ultimate end result for this product, we designed the product to suit injection moulding manufacturing process from the start, considering aspects such as wall thicknesses, ribs details and draft angles. This would later mean a fairly straight forward conversion from Vacuum Casting to Injection Moulding.
​
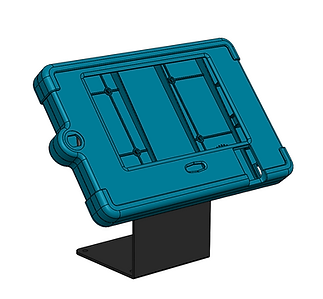


PROTOYPING & TESTING
Throughout the design process, various parts of the design were 3D printed to test factors such as the overall fit and strength characteristics. With our ability to 3D print in house, we were able to 3D print parts of the design, carry out testing and implement improvements, all within the same day.
​


Finally, once were were satisfied with all aspects of the design, a final 3D printed prototype was created using the Multi Jet Fusion (MJF) 3D printing process. This new 3D printing technology is great for final 'sign off' prototypes as it provides a smooth surface finish comparable to injection moulding, whilst offering strength and mechanical properties comparable to mass production materials. This fully functional prototype would be supplied to the customer for final feedback and sign off prior to production.
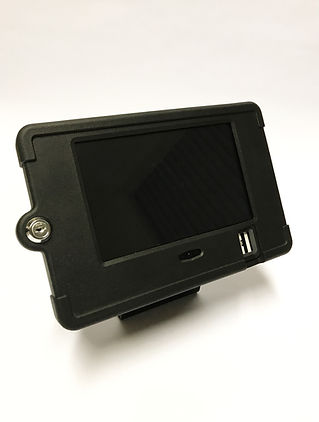


INITIAL PRODUCTION
Once the customer had approved the design, detailed engineering drawings were created to aid the manufacture of the parts. These would note important dimensions and tolerances as well as critical fits, surface finished etc, which would be critical to the correct function of the product.
​
Once completed, production could begin. The Vacuum Casting process involves creating a highly detailed and completely smooth 3D printed 'master' of the design using the Stereolithgraphy (SLA process) which would then be used to cast a silicone mould. Under vacuum this silicone mould would then filled with a pre-mixed resin which would set overnight. The following day, the parts would be removed from the mould and finished by hand. Each silicone mould is capable of creating up to 25 parts, ideal for low volume production. Like injection moulding, vacuum casting also allows inserts to be placed in the moulds and set in the product. In this case, 3 nut inserts were used.

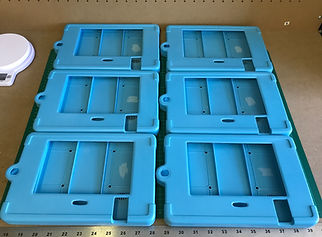
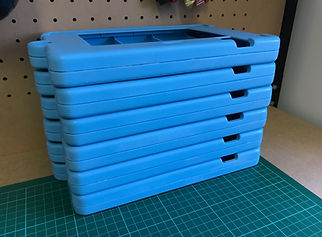
Print My Part excel at providing a complete service, and in doing so ensure every aspect of the project is taken care of. For this project, this included product assembly and sourcing of individual boxes so parts could be packed and shipped to end customers.
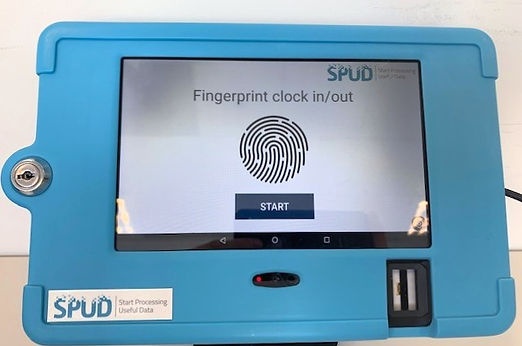

MASS PRODUCTION
Following a successful roll out of the Vacuum Casted units, with minimal design changes we were able progress with injection moulding the enclosure. This would ultimately result in a higher quality and more durable product, manufactured with exact repeatability. Using our close manufacturing contacts in China, we were able to support our customers demands to turn the tooling manufacture around very quickly to ensure an initial quantity of parts was manufactured prior to the Chinese New Year shutdown. The leads times and quantities in question would not have been possible using traditional UK injection moulders.
​
With our expertise in bringing product to market, we were able to take care of the complete manufacture process from tooling manufacture and review, through to quality control and hassle-free import. Once we were happy with the quality of the manufactured goods, parts were shipped and assembled in the UK, allowing us to carry out 100% quality control checks on every product to ensure excellent quality and functionality before personally delivering the goods to our customers premises.
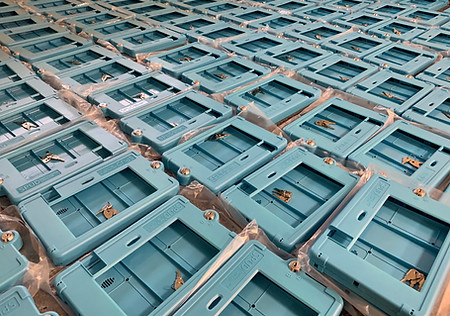

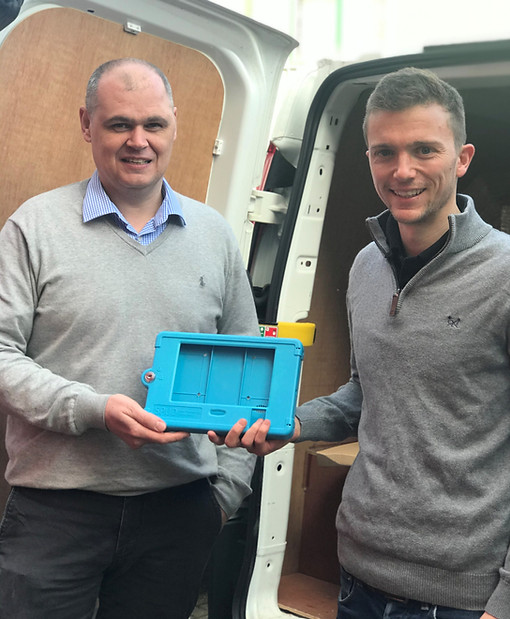
CUSTOMER REFERENCE
"We engaged Jack to explore the probability of producing a stand for our bio-metric tablet which are used for access control on our customers construction projects.
Jack excelled at every point of the design and manufacturing process, from his wealth of knowledge to his understanding of the quality control process we were furnished with information at every point of the process. The service offered has encouraged us to retain Jack on all future design projects as we are now moving manufacturing off shore and Jack still continues to show a vast knowledge of the manufacturing process outside the UK.
We would highly recommend Jack and Print my Part for your project, his skills in design, management, NRC, and delivery to schedule are impeccable".
​
Paul, Company Director
To discuss your product design requirements, please get in touch at info@printmypart.co.uk.